So you want to join the Kingston Potters’ Guild? There are three types of membership to choose from but you can only have your name on one waiting list:
Membership – $80.33 (+HST) / year
Membership with Glaze & Kiln Rooms Access – $171.36 (+HST) / year
Membership with Full Studio Access – $321.30 (+HST) / year
What does it mean to be a Member?
The Guild relies on the contributions of all Members to keep it running. Once you join the Guild as a Member, you will be assigned one of the available jobs, which range from organizing publicity to cleaning parts of the studio. You cannot be a Member without participating in Guild operations in some way. Members must be 18 years of age or older.
Often on Wednesdays, when there are no scheduled classes or meetings, members meet to work on their projects and talk about pottery stuff. You are welcome to join. It’s a good moment to meet members and ask questions you may have. We encourage you to sign-up on our Facebook Kingston Potters’ Guild Members Forum page. If you join a committee you will meet others too.
Our Guild meetings are on Wednesdays, and attending them helps you learn about how we function as a group. We would ask that you attend a minimum of three of these (there are only six per year).
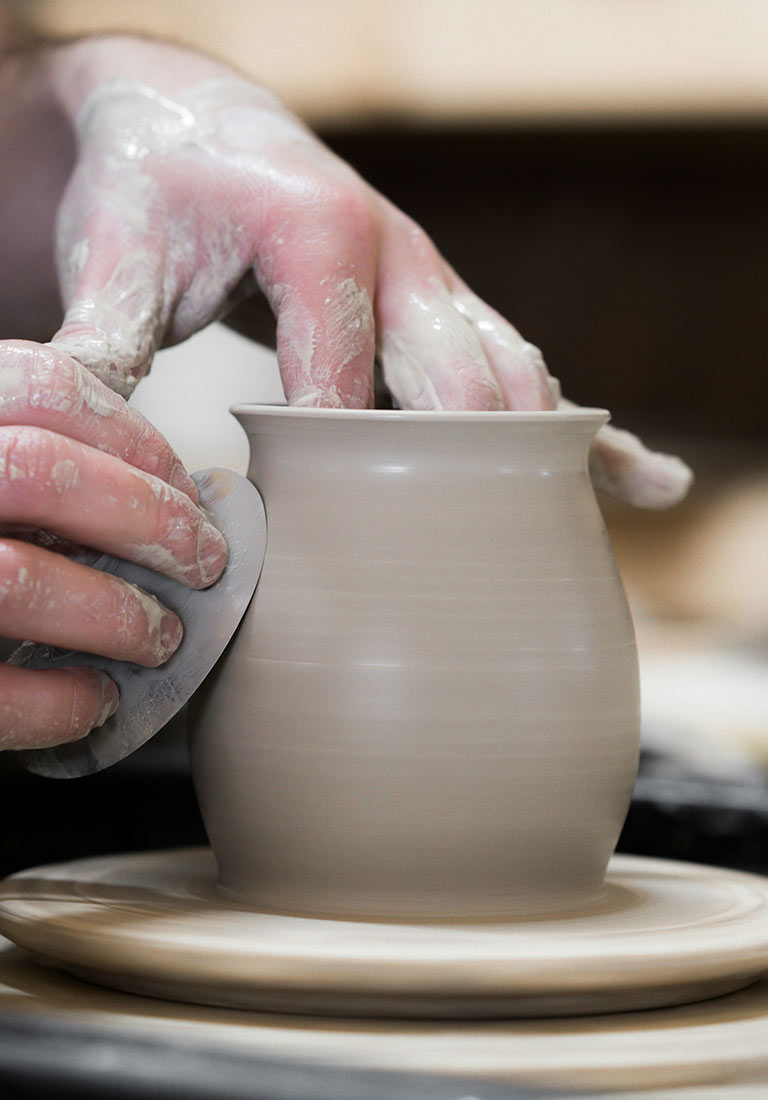